
Robert Eddy
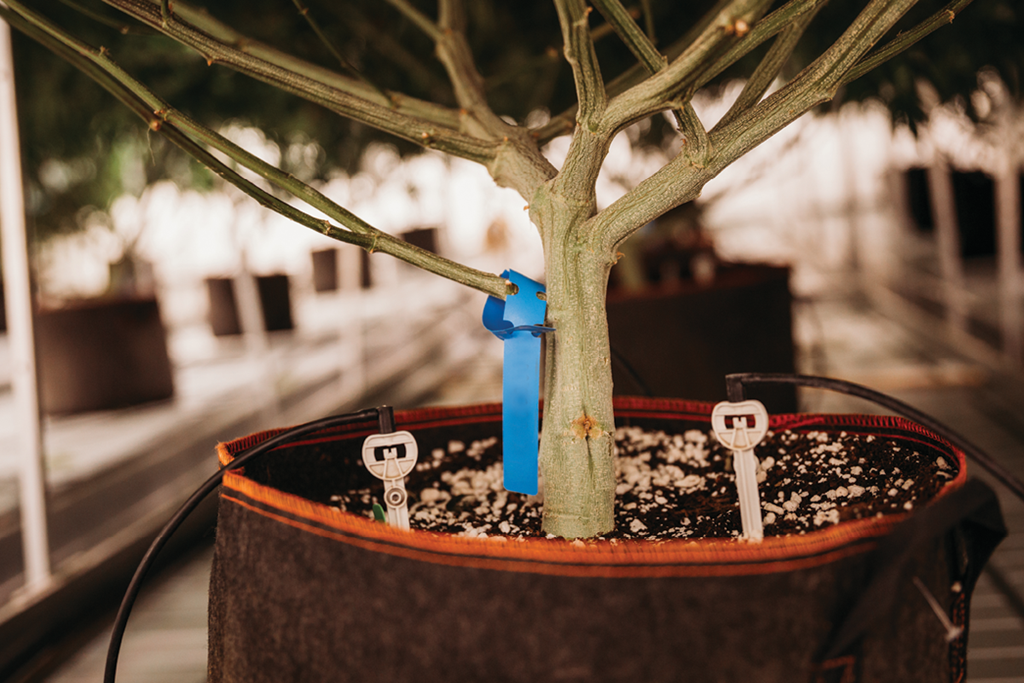
Hydroponics has varied definitions, yet all of them have one phrase in common: growing plants in a soilless nutrient solution. Practically all indoor plant production is performed using a rooting substrate, not soil. (Soil is the upper layer of earth that can be plowed and in which plants grow (aka dirt).) You may be familiar with equivalent terms for rooting substrate, such as artificial media or aggregate; but for clarity, I will refer to it as substrate for the remainder of this article.
If your substrate doesn’t contain mineral soil and you are adding fertilizer solution to it, you are growing hydroponically. Hydroponics also requires some form of automated irrigation to keep up watering needs. Dr. Chris Currey, a hydroponics expert at the University of Iowa, points out that hydroponics is often characterized by a low root:shoot ratio—a big plant in a tiny container.
Many cannabis growers grow hydroponically, and the substrate is merely there to keep the plant erect. This is especially true if the substrate is inert, meaning it does not react chemically with the solution or the roots. Specifically, an inert substrate doesn’t affect the pH or electric conductivity (EC), and it doesn’t have an electrical charge to hold nutrients for later release. This electrical charge is quantified by the cation exchange capacity (CEC). If your substrate has a low CEC, it is chemically inert. Perlite and rockwool are examples of practically inert and inert substrates, respectively.
Examples of hydroponic substrates with high CEC (that are not inert) are peat moss and zeolite. Coir and vermiculite have a somewhat lower CEC.
Inert substrates can’t readily hold nutrients, so they are less likely to accumulate fertilizer, and the crop may require nutrient renewal every irrigation. Inert substrates also are less likely to accumulate salts that could damage roots. Their minimal effect on pH means you must more precisely manage your nutrient solution pH because there is nothing to buffer the roots from an immediate change in pH upon irrigation with an acidic or basic fertilizer—the same as if you were growing in water-based hydroponics.
The point is: Indoor, containerized plant production is more similar to growing plants in water than it is to growing plants in an outdoor garden, and your management practices must follow suit. Water, pH and electrical conductivity (EC) of both the nutrient solution and the substrate must be closely monitored and adjusted. The importance of routine substrate monitoring cannot be overstated. A good monitoring method is the non-destructive pour-through method. (For more information on the pour-through method, visit: bit.ly/pour-through.)
The payoff for this monitoring effort is the ability to make decisions based on data, resulting in faster growth and higher yields. The good news is that there is no reason to reinvent the wheel. The vegetable and floriculture (flowering crops) industries have been solving these problems and developing soilless plant growth methods since Cornell University developed its Peat-Lite mixes in the late 1960s.
Though substrate-based hydroponics has become popular in the greenhouse industry over the past 50 years, technological advancements in water-based hydroponics systems have come in bursts, spurned by new technologies that help overcome the increased costs for fertilizers, plumbing, containers and lighting. There was the advent of a balanced formula for nutrients solutions that plants could grow in by Dennis Robert Hoagland and Daniel Israel Arnon in 1938. The 1960s saw the hydroponics industry overcome the high costs of concrete planting beds and metal plumbing and emitters by adopting plastics. A decade later, rising oil prices wiped out the burgeoning hydroponics industry thanks to a cost increase in energy. Today, innovations in powerful light-emitting diode (LED) lighting and microprocessor control of environments have led to another era of hydroponics growth and accessibility.
Fueling hydroponics’ growth is consumer demand for locally grown produce with fewer pesticides and less water waste and for safe medicinal and recreational cannabis cultivars. LED lighting, with improved energy efficiency, slim fixture profiles and indirect heat load, has single-handedly spawned new hydroponics forms—”multi-tier” or “vertical farming”—that weren’t possible 15 years ago.
Here is a rundown of common substrate-based hydroponics systems in use today:
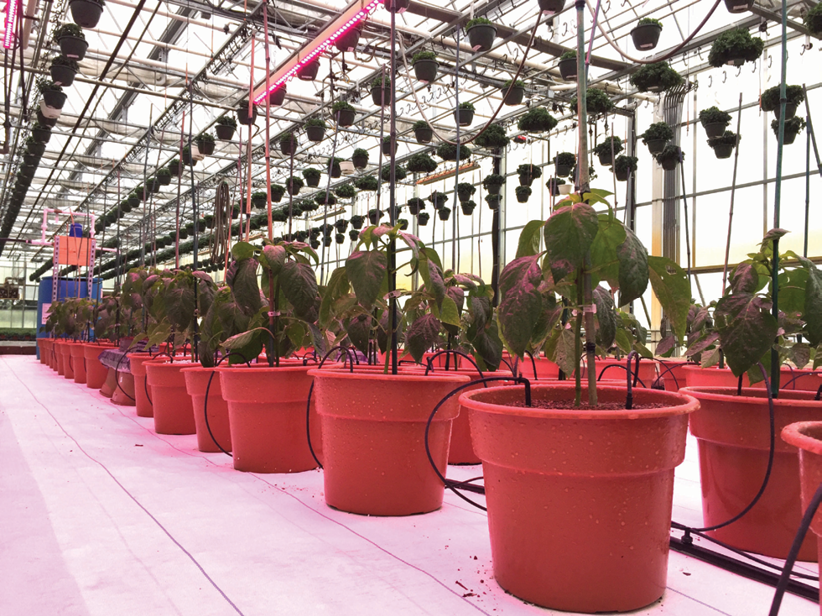
Drip-Irrigation
In drip-irrigation systems, nutrient solutions are automatically fed into irrigation lines using a fertilizer injector drawing from concentrated fertilizer tanks or pumps drawing from reservoirs of pre-mixed solutions. Often, a combination of locally purchased solenoids, PVC-pipe, polytubing, manifolds and garden hose delivers the solution to the growing table or planting row. Specialized irrigation components deploy the solution to the containers via distribution tubing and drip emitters, stakes or sprayers. Irrigation is triggered by either a timer or a computer that is monitoring a weight scale, a soil moisture sensor or an environmental parameter, such as accumulated light. Plants grow in pots, grow-slabs or grow bags. The substrate typically is peat, coir, rockwool, vermiculite, perlite, bark, wood fiber or clay pellets, or a combination thereof.
The volume of water applied at each irrigation is typically set to achieve a 30-percent leaching fraction. A leaching fraction is the amount of water applied beyond what is needed to saturate the substrate (overwatering) that helps rinse out or “leach” accumulated fertilizer salts. For example, if each irrigation typically requires 200mL of solution before your substrate begins to drip from the bottom of the container, a 30-percent leaching fraction would mean you apply 260mL (200 + (30 percent of 200) = 200 + 60 = 260).
Leaching fractions are not static and should be adjusted according to the crop, the stage of development and the weather (if you’re growing in a greenhouse). Your routine EC testing of the substrate will indicate if fertilizer is accumulating or being depleted, requiring an increase or decrease in leaching fraction, respectively. Some computer-control systems automatically monitor the leachate pH and EC and adjust the irrigation system accordingly.
Excess water in drip irrigation systems can either be captured and recycled or drained to waste, depending on state and local regulations. Recycling for this system, or any system mentioned in this article, requires recapturing leachate via tables or troughs with drains and holding it in a reservoir, where it must be disinfected, pH-balanced and perhaps replenished before reapplication.
Drip systems are easy to install as DIY projects. They typically result in higher substrate moisture content throughout the crop’s life than hose watering, but lower soil moisture and relative humidity over time when compared to sub-irrigation. Drip system challenges can include clogged drippers and leaks from the multiple connection points. Biofilms, or microorganism (e.g., bacteria) layers, may need to be controlled using disinfectants between crops. One method to prevent clogging and biofilm accumulation is to install clean-out valves on the ends of the dripper feed lines to force full-pressure water through every week or so.
Ebb-and-Flow
Ebb-and-flow, also called flood tables, is often used in cannabis vegetative rooms, even if the flowering rooms have drippers, due to high density of vegetative plants that preclude drippers. Nutrient solutions fill the table at a defined depth and interval then drain back to a reservoir for treatment and reuse.
Ebb-and-flow may result in a more uniformly wetted substrate than drip irrigation, as the substrate absorbs the liquid upward through capillary or “wicking up” action, eliminating dry spots sometimes observed between drip emitters. These systems have fewer connections and parts than drip systems and are easier to maintain and observe throughout operation. Proper leveling is required to fill the table evenly while still allowing for a slight slope toward the drain—the longer the tables, the more important this is.
Any standard substrate that can be used for irrigation (such as rockwool, peat, coir and soilless mixes) can be used for ebb-and-flow. The amount of water absorbed upward is determined by the physical properties of the substrate, such as its water-holding capacity. Furthermore, the substrate grade (meaning: to what particle size it has been formulated) and the container height also affect capillary action. For example, though they are made from the same material, coco chips will not wick up to the same height as finer-grade coco fibers. Too large a particle size or too tall a pot, and you won’t wick water completely up, no matter how long the container is partially submerged.
When fertilizing in any sub-irrigation system such as ebb and flow, it is more difficult to remove fertilizer salts that may accumulate in sub-irrigation. Use about one-third less fertilizer in your nutrient solution than you would if irrigating the same crop from above. Test your levels weekly at minimum.
Ebb-and-flow is often used in vertically stacked grow racks inside shipping containers. These air-conditioned containers are becoming popular in both the leafy green and cannabis industries. Often, the nutrient solution flows from one level to another before gravity pulls it to the reservoir below. This requires more balancing of the flow and drain rates to avoid overflowing or dry shelves.
For larger systems in greenhouses and grow rooms, size the pumps and drains correctly to reduce the time plants are sitting in water. Typically, it takes only a few minutes for substrates to absorb water up the full column of your container. The faster you can get the water in and out while still saturating the substrate, the less likely you’ll spread root pathogens (like root rot) from one pot to the next. For this reason, keeping the drains clog-free is important.
Challenges that can be associated with ebb-and-flow systems include algae growth and a higher likelihood for fungus gnats or shore flies. Any sub-irrigation system I have ever used has resulted in a wetter substrate and fewer irrigations over the life of the crop. It simply saturates the substrates more effectively each time, so they stay wetter longer—and wetter substrates are conducive to these pests. Also, sub-irrigation systems will raise humidity more than drip systems.
Capillary Mat
In a capillary mat system, substrate containers sit on an absorbent mat, typically kept moist by thin-walled distribution tubing with holes. The mats range from simple felt rolls to multi-layer specialized products. Substrate wicks up the nutrient solution through the holes in the container’s bottom. This is a simple system with fewer parts and fittings than drip irrigation and without the balancing needed for ebb-and-flow. Any table can be modified using a plastic liner under the capillary mat. It’s most useful in an environment with very high plant densities. It’s also useful for plants with a constant water demand due to small container volume.
Challenges of capillary mats can be serious: algae build-up, fungus gnats and shore flies, and high humidity are all risk factors when using this type of system. Additionally, adequate contact between the substrate and the wet mat needs to be maintained.
One of my favorite tricks with capillary mats is to make self-watering trays with no mechanical parts that can go afoul. To make a self-watering tray, submerge one end of the mat in a tub of water or nutrient solution and spread the rest over a tray. Place planted seedlings or clones directly on the mat, ensuring contact with the substrate. This maintains even moisture and also creates a high humidity environment for rooting. If done correctly, it can easily sustain your crop through that entire weekend you are hoping to enjoy!
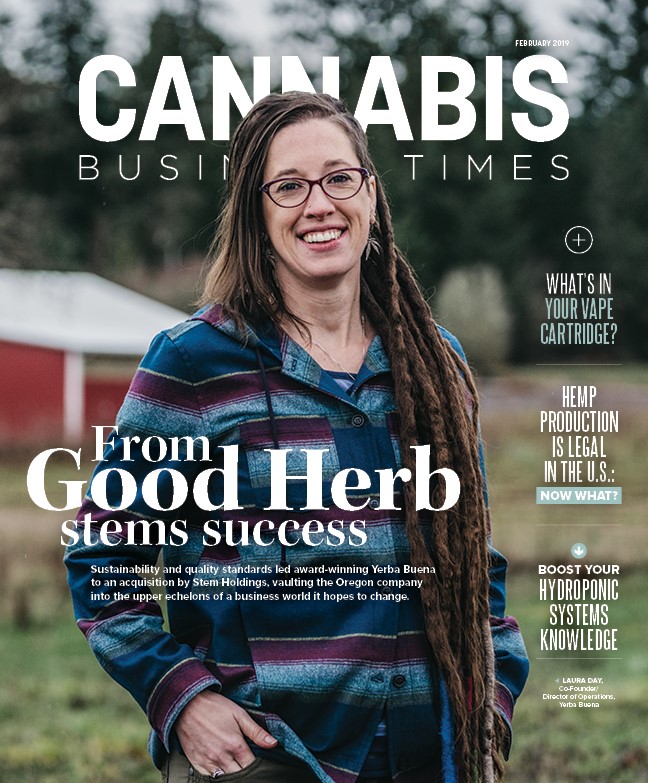
Explore the February 2019 Issue
Check out more from this issue and find you next story to read.
Latest from Cannabis Business Times
- South Dakota Group Submits 29K Signatures for 2024 Adult-Use Cannabis Legalization Measure
- Rescheduling Would Have Saved Verano $80M in 2023 Tax Payments, CEO Says
- Aurora Marks 1st Medical Cannabis Shipment to New Zealand Market
- Where All 100 US Senators Stand on SAFER Banking Act
- Blumenauer Unveils Legislative Blueprint, Additional Administrative Action Needed Following Rescheduling
- Cannabis Rescheduling FAQ: What Now?
- From Custodian to Cultivation Supervisor
- California City in Cannabis Retail Desert Welcomes 1st Dispensary