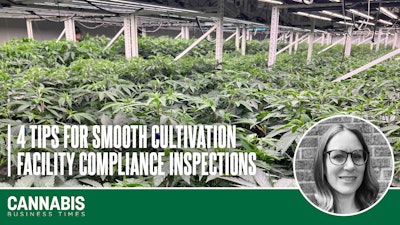
Failing a cannabis cultivation facility inspection can result in fines and other disciplinary actions, from suspensions to license revocations, that can ultimately derail one’s business.
These disciplinary actions can come from myriad compliance issues, ranging from incorrect inventory tracking to inadequate surveillance systems, unreported physical modifications to a building, improper waste disposal, out-of-date employee badging, and even incomplete visitor logs.
In Michigan, for example, state regulators issued more than 100 citations in January to dozens of businesses across 33 jurisdictions. Michigan’s compliance penalties include $10,000 for failing to submit timely financial statements, $10,000 for inaccurate inventory tracking, $10,000 for failing to meet security requirements, and a long list of other infractions.
Cannabis businesses that take compliance seriously and work compliant practices into their regular operating routines can avoid these costly and sometimes time-consuming penalties. Here are four tips for cultivation facilities to help ensure smooth inspections in this highly regulated industry.
Tip 1: Prepare and Practice
Bins labeled and organized at Galenas.Photo by Christine DeJesus
Conduct counts of plants and packages close to the inspection date so that records reflect current inventory. Log any inventory adjustments and have these records available for reference at the time of inspection. Confirm that all plants and packages have appropriate tracking tags and that any printing on tags is accurate and legible. Per state regulations, if required, verify that plants are not out of compliant height range if untagged, and tag plants or trim down to the required height when necessary. Confirm that all regulated product packages are tagged and stored properly. Waste disposal logs are often closely scrutinized, so check to make sure dates are in order and forms are accurately completed.
Schedule all responsible parties to be present on the day of inspections. To prepare for surprise visits, maintain coverage to ensure that at least one prepared, responsible employee is present on any given workday. Remind staff about regulations that may allow for employee lockers, personal belongings, and personal vehicles to be requested for search during compliance inspections. Employees should all have current identification badges. Confirm correct access privileges on door swipe keycards. Ensure that employee training records are updated, as well as sanitation and equipment maintenance logs, and verify the accuracy of the facility employee personnel roster.
Make sure that all security cameras are functioning properly, including outdoor cameras on the facility perimeter. Check outdoor lighting functionality. If applicable, check in-house delivery vehicle documents, including vehicle tags, driver’s licenses, insurance policies, and service records, and visually assess delivery vehicles for cleanliness and compliance.
Conduct a dress rehearsal. Walk through a mock inspection with responsible employees. Slowly moving through the facility with an eye toward compliance issues often alerts personnel to something that was missed in preps.
Tip 2: Clean House
Ohio-based cannabis cultivator Galenas' facility cleaning and sanitation log.Photo by Christine DeJesus
Support rooms like bathrooms, kitchens, and break areas should always have strong sanitation standards and well-stocked supplies. Double-check that nothing in support rooms has been missed in the cleaning rotation, such as coffee stations, microwaves or other small appliances, kitchen supply areas, and vending machines. Freshly stock items such as toilet paper, hand towels, and personal protective equipment (PPE) as needed.
The front desk is usually first seen, so make sure it’s uncluttered and organized and visitor logs and visitor badges are accessible and accurate. Less-utilized areas may get overlooked and can use a check-up. Think of spaces like electrical and maintenance rooms, information technology (IT) rooms, staff offices, and storage areas. Check loading docks, trash storage areas, outdoor storage structures, and pest control equipment for cleanliness and proper functionality.
Confirm that the entryway is unblocked and free of snow or debris and parking lots are well maintained. An added perk is an open parking spot or two close to the front door on inspection day for compliance agents. First impressions are important, and adding a welcoming touch can go a long way.
Tip 3: Respect the Inspector
Organized PPE at Galenas.Photo by Christine DeJesus
Preemptively eliminate issues that could make the inspection take longer than necessary. Proper organization of records can streamline the process, and eliminating cluttered areas or disorganized storage spaces in advance will avoid wasting the time of regulators. If enterprise resource planning (ERP) software or a web-based project management tool is used for task tracking, consolidate lists and print out reports or streamline digital access. Cleaning logs, maintenance records, and employee training records can be entered into an edited tab or format explicitly available for compliance inspections.
Take the inspection seriously. Remain calm throughout the process and provide full attention. For the responsible party involved, personally pausing the daily work schedule, muting notifications, and avoiding distractions can further communicate respect. Provide a quiet office or area with an open working space for document sharing and one-on-one or private conversations.
Tip 4: Study the Regs
Harvested flower at Galenas.Photo by Christine DeJesus
Larger companies often maintain a compliance team member or consultant who specializes in staying abreast of regulations. Legal experts can often best interpret the complexities of evolving regulations. Smaller businesses may handle this internally, in which case it is important to dedicate time and resources to tuning in to updates and changes. Regulations form company policy, and policies require updates when procedural or operational changes are made or regulations are adjusted or added.
Subscribe responsible employees to messaging and notifications from regulators and meet regularly to discuss which changes impact the facility and team. Ask for help when a rule or change needs more clarification. Many regulatory bodies have a service center for questions, or inspection agents are available for follow-up. Attend METRC or state regulatory update-and-training sessions. Sending a responsible employee to a training session shows a dedication to compliance. Provide an open channel of communication and stay on top of required responses.
During the inspection, ask regulators if there are any new changes that the facility should be aware of. Most importantly, make compliance part of your regular routine, with sound protocols and processes to avoid falling behind in any one area. Take compliance seriously. Deficiencies can be costly and lead to additional time-consuming inspections. In a highly regulated industry like cannabis, it is key to the success of the business to remain in good standing with state compliance.
Christine DeJesus is the General Manager at Galenas in Akron, Ohio.