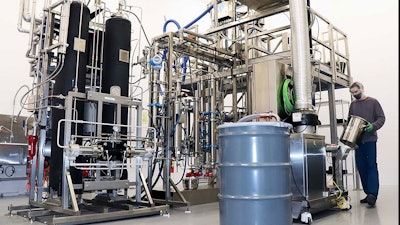
Co-solvent CO2 systems have emerged as an efficient tool for extracting desired cannabis compounds at scale. Combining the versatility of liquid CO2 with the scalability of ethanol, these units can help large-scale businesses rapidly process large amounts of biomass while delivering a wide range of products to consumers.
Here, Kiran Dayaram, Research and Development Consultant at Vitalis, offers four essential tips to help cultivators and processors get the most out of a CO2 co-solvent extraction system.
1. Decrease CO2 pressure and temperature to extract terpenes and aroma compounds.
Historically, CO2 extractions ran at higher pressures and temperatures. Vitalis’s CO2 extraction system offers operators the versatility to leverage cold liquid CO2 at low pressures, enabling operators to create a wider variety of products more efficiently.
“At low pressures, you will get a more targeted extraction. You will extract a lot more volatile compounds, your terpenes, esters, and aldehydes,” Dayaram explains. “If you're running under about 10 degrees Celsius, you're going to improve the quality. The colder you go from there, the better it gets.”
Cold extraction can be augmented with the addition of a co-solvent following the volatile organic compounds (VOC) extraction to target different compounds.
2. Increase CO2 pressure and temperature, as well as co-solvent flow rate, to extract more fats and waxes.
Increasing the CO2 pressure that runs through your extraction system will typically allow you to extract more compounds in a run, Dayaram notes. “At higher pressure, you're going to get a lot more of your waxes and fats, and that's going to make a more viscous extract,” he explains.
Similarly, increasing CO2 and/or co-solvent temperatures also will pull more compounds from the cannabis being extracted. If VOCs aren’t extracted in a first cold run, they will be extracted with the co-solvent—typically ethanol—and separating the VOCs from the cosolvent is difficult and deleterious on the aromatics.
Increasing co-solvent flow rates also will increase the variety of compounds getting pulled into the oil. “Typically, most people operate in a range of 1% to 10%,” Dayaram says. “You can go higher than that—there are papers you can find that go up to 30%,” he continues, “but you start to lose some of the nice things about co-solvent extraction above 10%,” such as being able to precisely target the compounds you want to extract vs. those you want to leave behind.
Terpene-rich extracts can be made by extracting terpenes and other aromatics first, while distillates can be made by extracting cannabinoids at higher pressures and temperatures.
3. Consider operational goals and desired outcomes when determining CO2 pressures and temperatures.
Finding the right balance of pressure, temperature, and co-solvent rate is the key to maximizing co-solvent system efficiency. As pressure, temperatures, and co-solvent flow rates increase, “you start to get into the problem of chlorophylls and other unwanted compounds” entering your extract, Dayaram says.
Pressures also determine the amount of co-solvent you’ll need to achieve a desired outcome, which can increase operating costs. “What we've found is, typically, in your lower pressure, you need a lot more ethanol to achieve the same extraction endpoint as you would at a higher pressure,” Dayaram shares. “But there's also a flip side that if you go too high, then you get a lot of co-extraction of undesirables. So there's a sweet spot sitting in the middle in terms of pressure.”
At the lower end of co-solvent injection, operators can achieve a more selective extraction process that still reduces extraction times compared to a CO2-only extraction. “It comes down to, do I want to make my extractions faster, get everything out a little bit faster, and have a little bit more post-processing on the back end? Or would I rather make my extractions longer [but have less post-processing work to do?]” Dayaram asks.
4. Add in-line refinement to increase extraction process efficiency.
Because co-solvent extraction can increase throughput by up to a factor of four, bottlenecks can occur during downstream refinement, especially with winterization and solvent recovery.
Airo, Vitalis’s automated in-line refinement system, addresses this issue by allowing operators to replace up to seven different pieces of equipment and/or post-extraction refinement steps. With Airo, manufacturers can produce up to 20 kilograms of refined extract every two hours, which can minimize or eliminate bottlenecks. “Depending on how much ethanol you use per extraction and your system size, one Airo system holds up to eight extractions,” Dayaram notes.
The Airo system is “modular, so you could piece it together depending on how far down the post-[extraction] process you wanted to go,” he explains. “The first module is winterization, the second module is color remediation, and the third module is solvent recovery. Then you can have decarboxylation, and then a final solvent recovery step.”